Warp Knitting Machine Parts Explained: What You Need to Know
Warp knitting machines play a vital role in the textile industry by producing fabric quickly and in large quantities. These machines consist of numerous small components, each performing a specific function. For instance, the needles are responsible for forming loops, the guide bars direct the yarn, the sinkers hold the fabric in place, and the take-up and let-off systems regulate the fabric’s movement through the machine.
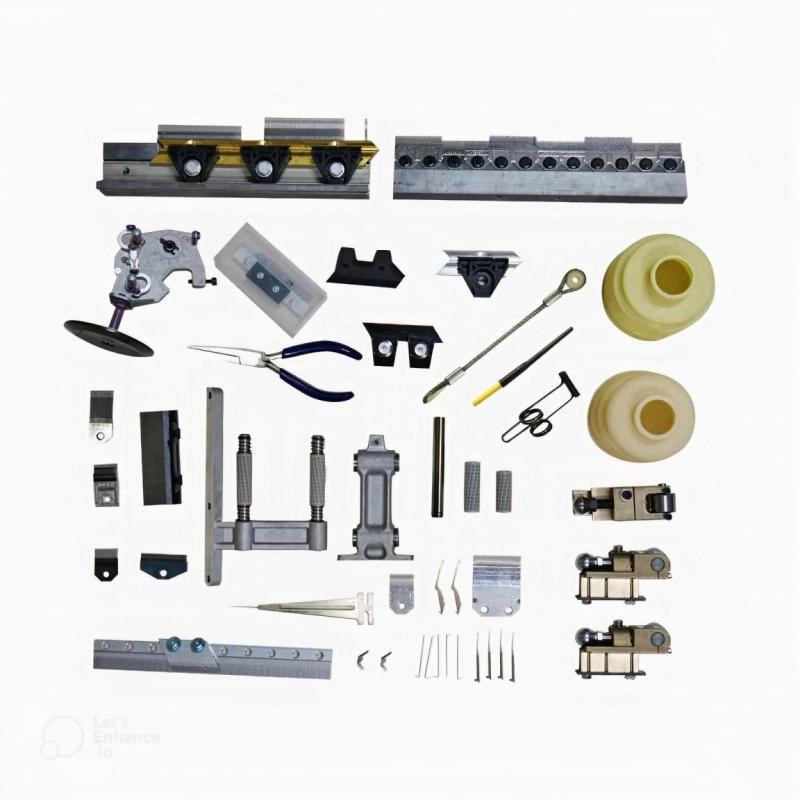
Proper maintenance of these parts is essential. If any component malfunctions, it can halt the entire operation. That’s why regular cleaning and inspection are crucial. Operators should be familiar with every part of the machine and be capable of handling minor repairs. This not only minimizes downtime but also reduces costs.
Curious about how each part works and why it’s important? Let’s take a closer look!
Core Components of a Warp Knitting Machine
Needles
The Warp Knitting Machine Parts begin with the needles. They help make loops in the fabric. These loops build the cloth. Each needle works fast and needs to move in the right way. The shape and size of the needle matter. If the needle breaks, the cloth will not look good. So, it is important to check them often.
Guide Bars
Next, the guide bars help the yarn move to the needles. They move side to side. This helps make different fabric styles. The bars need to be in line with the needles. If they are not, the yarn may break. This may stop the machine. So, the guide bars are also very key Warp Knitting Machine Parts.
Sinkers
The sinkers hold the cloth in place. They work with the needles. When the loop is made, the sinkers stop the fabric from moving too much. This keeps the fabric tight and smooth. Sinkers must move at the right time. If they are too slow, the loops may not form well. They are small, but they play a big part in the machine.
Supporting Mechanisms That Make It Work
Take-Up Rollers
The take-up rollers pull the fabric out of the machine. After the loops form, the rollers move the cloth forward. This makes space for new loops. The speed of these rollers must match the rest of the machine. If they go too fast, the cloth may stretch. If they are too slow, the machine can jam.
Let-Off System
The let-off system gives yarn to the machine. It keeps the yarn tight, but not too tight. If the yarn is too loose, the loops may be weak. If it is too tight, the yarn can snap. This part works with the yarn beam. Together, they help control how much yarn goes in. This makes it a key part of the Warp Knitting Machine Parts.
Cams and Gearing
Cams and gears control when the parts move. They help each part move at the right time. This timing is very important. If one part moves too soon or too late, the loop may not form. That can cause fabric errors. So, cams and gearing must be set well and kept in good shape.
Maintenance Matters: Keep Your Machine Running Smoothly
Regular Cleaning
Cleaning is very important. Lint and dust build up fast. This can block parts and stop the machine. A quick clean each day can help a lot. Use soft brushes and air to remove lint. This small task helps the machine last longer.
Lubrication
Moving parts need oil. If they are dry, they can wear out. A few drops of oil at the right spots can stop this. Do not use too much. Just enough to make the parts move smooth. Clean first, then oil. This keeps the Warp Knitting Machine Parts in good shape.
Part Replacement
Some parts wear out over time. It is best to change them before they break. Keep a list of when parts were last changed. This helps plan ahead. A broken part can stop work for hours or more. But changing it on time keeps things running well.
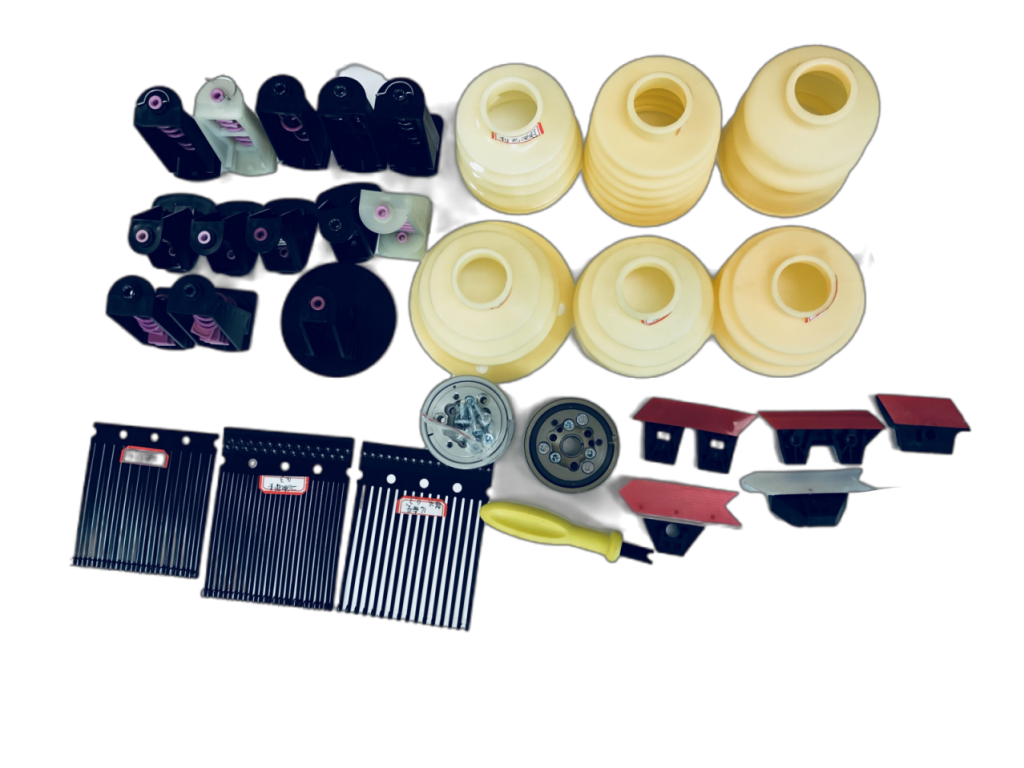
Meet Grand Star Technology: A Global Trusted Manufacturer
Our Beginning and Team
Grand Star Technology started in September 2012. The company makes warp knitting machines and control systems. It is based in Fuzhou, Fujian. The team includes over 50 skilled workers. Each person has a clear role. We focus on building strong and useful machines. The company also puts effort into research and design. This helps improve every part of the machine. These include key Warp Knitting Machine Parts like needles, guide bars, and control systems.
Global Reach and Growth
The company now works with clients in many countries. These include the United States, Japan, Turkey, Vietnam, Indonesia, India, Colombia, and Mexico. Grand Star has grown by building trust. It offers quality machines that last. The parts are made with care and tested well. This helps customers use them longer. The company follows global quality rules, like ISO9001. It also uses smart design tools. These tools help make better Warp Knitting Machine Parts with fewer errors.
Focus on Precision and Quality
Grand Star is known for precise parts and green solutions. The machines save power and work fast. The company also offers help after the sale. Clients get support if parts need to be replaced or fixed. This builds long-term trust. All parts, big or small, are made to fit and work well. These include both main parts and support systems. Because of this, Grand Star is a top name in the field.
Innovation Spotlight: The Warping Static Eliminator
What It Does and Why It Helps
The Warping Static Eliminator removes static during warping. Static can stop the yarn or cause breaks. This tool works better than older methods. It lowers yarn issues and cuts machine stops. Less downtime means more work gets done. The eliminator fits into most setups. It is easy to place and does not need big changes. This makes it useful for many machines that use key Warp Knitting Machine Parts.
How It Works
This tool uses high-voltage discharge. It sends out ions to balance the air. These ions remove static from the yarn. The tool works in a range of 30–50mm. It keeps yarn smooth and clean. There is less kinking and pilling. Yarn breakage is also less. This makes the fabric better and saves material. It is more steady than older tools, which may not work the same every time.
Where It Should Go
The eliminator works best in key spots. These include above the reed bracket and near the tension device. It also works well near the warp break stop and the rear reed. In these areas, static often builds up. Placing the eliminator here keeps the yarn straight. It also helps measure warp length better. These small changes help the whole machine work better and protect other Warp Knitting Machine Parts from extra stress.
Why This Knowledge Matters
Good Parts Mean Better Results
Picking the right Warp Knitting Machine Parts is key. It helps make strong fabric. It also helps the machine last longer. Broken parts slow down work. Good parts help keep the machine running. They also help save time and money.
New Tools Help You Compete
Knowing about new tools gives you an edge. Machines with new parts work faster. They break down less. This means more fabric is made. Staying updated helps you stay ahead of others. It also helps you fix problems early.
Working with a Trusted Name Helps
A strong maker like Grand Star gives you peace of mind. You know the parts will work. You also know help is there if needed. The company supports many users worldwide. They keep making better tools and parts. This helps many kinds of textile work.
Upgrade with Grand Star‘s Warp Knitting Machine Parts
Enhance your production with high-performance parts from Grand Star Technology. Built for strength, precision, and durability, our warp knitting machine parts are designed to improve fabric quality and boost efficiency. Each component fits seamlessly, operates smoothly, and is easy to install.
Trusted by professionals worldwide, Grand Star ensures every part is thoroughly inspected before shipping—so you receive reliable performance, right on time. Looking to upgrade your machines? Choose Grand Star Technology‘s warp knitting machine parts and experience smoother operations, day after day.
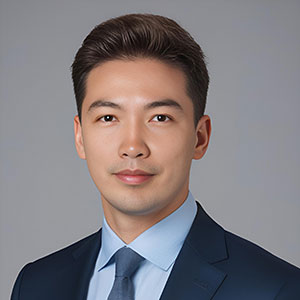
Hey, I’m Vincent!
Solving complex challenges with precision and creativity in the warp knitting industry. Passionate about advancing textile engineering and turning innovative ideas into reality. Shaping the future of warp knitting.